Dec Philosophy
Process Linking
Active vs passive charging
​
​
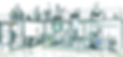
Process Linking - From Batch to Semi-Continuous Process
Batch manufacturing is still commonplace in the pharmaceutical and chemical industry. Such operations require to use intermediate packaging for product storage between each process step leading to low production flexibility, high process downtime, high risks of operator exposure, product contamination and sterility loss.
​
​Dec's way to improve productivity, safety and containment at the same time is to interconnect production equipment in a closed way (i.e. discharging a centrifuge directly into a dryer or a reactor, direct charging from a blender to a tablet press, etc.).


​
Dec's innovative solutions to change pure batch processes into semi-continuous operations provide flexible and multipurpose facilities which are cGMP compliant with adaptable containment levels.
​
Linking processes together decreases batch failures due to better control of the production with less human intervention. It minimizes downtime and energy consumption with fully automated CIP/SIP systems. The overall foot print of the plant will also be reduced by decreasing the number of process steps.
As opposed to gravity charging, PTS Powder Transfer System® allows to convey powders over long distances without segregation or particle damages and can therefore link different process equipment without problems. PTS can transfer dry and wet powders directly out of process equipment and charge it in a closed way into the next process step.
It is also possible to automatically feed from one process equipment more than one apparatus (i.e. charge a few reactors from one single big bag emptying station) or feeding from a few systems to a single station (i.e. multiple dryers discharge into one filling station).
In order to guarantee a totally contained operation, not only the transfer should be carried out in a closed way but also the cleaning operation. The complete process line including the process equipment, the transfer line and the PTS can be CIP’d and if required, SIP’d, at the same time.
Why you should link your processes :
-
Totally closed operation preventing cross contamination, product exposure (GMP compliant) and increasing safety
-
Full containment. Elimination of the requirement of a docking or containment system
-
Elimination of the requirement of a clean room
-
No intermediate storage required
-
Increased plant productivity with higher throughput
-
Decreased plant footprint and elimination of a charging floor
-
Possibility of complete automation of the process
-
Decreased number of process steps by interconnecting multiple equipment
-
Lower investments
-
Full CIP, SIP operation
​
Active vs Passive Charging
It is a common belief that the use of gravity to charge powder into process equipment is more economical posing less operation risks rather than using a more automated system.
However, experience has shown that this is often not the case and that the use of gravity could in fact lead to major safety issues and high operation costs.
​
Over many years, Dec has been developing and improving a concept to handle powder in a safe and contained manner without the use of gravity.
This concept is based on Active Charging - i.e. the use of energy to transfer powder - as opposed to Passive Charging where only gravity moves the powder.
The heart of this concept is the PTS Powder Transfer System® which uses vacuum and pressure to convey powder similar to the handling of liquids. This system can be used during various production stages, e.g. raw materials handling, charging and discharging process equipment and final product packing.

In order to decrease manual handling and improve operation, many industries, from pharmaceutical to chemical companies, are trying to elimitate drums and bags from operation by replacing them with FIBCs (flexible intermediate bulk container) or better known as big bags. However, handling such large packaging brings other issues in terms of safety and manufacturing flexibility.
In line with the latest safety, quality and containment standards, gravity charging is no longer accepted as the proper way to charge reactors, regardless the fact that it has been industry standard for many years. In order to charge a vessel by gravity from a top floor, a minimum of safety devices are required in order to guarantee the safety and process reliability while charging the powder (see article of Dr. Martin Glor - Swiss Safety Institute in the login section).
The advantages of this concept can be explained with a few examples.
​
PTS vs Big Bag Discharge for Reactor Charging by Gravity
To assure a permanent inert atmosphere in the vessel, isolating the powder system (i.e the big bag station) from the vessel atmosphere for instance by a rotary valve is mandatory. The rotary valve will also control the flow velocity which should be less than 1 m/s in order to avoid electrostatic charges in chutes exceeding 3 m. The chute itself should also be isolated from the vessel by a full bore type shut-off valve (ball valve, gate valve or segment valve) to prevent blockages and to guarantee the sealing of the reactor during the process. The chute should be inerted before, during and after charging. In case of corrosive atmospheres in the reactor, the chute and the valves should be designed with non-corrosive materials (HC 22, PTFE, etc.).Dec has solved above issues by using PTS Powder Transfer System® allowing to discharge big bags and safely charge reactors eliminating the need of a chute often leading to bridging, cleaning and safety issues. This simple and effective solution decreases overall investment whilst increasing both plant flexibility and productivity.
By installing the big bag station on load cells, PTS can directly transfer the required quantity of powder in the vessel repealing the need of pre-dispensing operations. The discharge station can also be located in a different area, i.e. not directly above the vessel as required for gravity discharge, eliminating the use of an elevator which can quickly become a bottleneck in a facility. It is also possible to have one single discharge station feeding two or more vessels thus further decreasing the investment cost.
By gravity method, big bags are required to be evacuated before disconnection in order to guarantee a dust free disconnection which implies a connection to an external extraction system. This arrangement is not required by using the PTS system as its vacuum will automatically evacuate the big bag and avoid product losses in the extraction system.