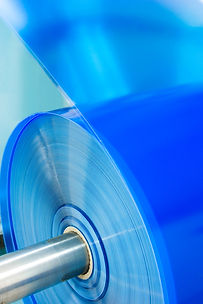
CLS Continuous Liner System
Closing devices, liner specifications and accessories
Dec can provide various closure devices depending on the level of containment to be achieved.
Standard Clip System up to OEB 3*
-
Closure tool device with specially designed cable tie system
-
Strong closure for different sizes of liner
-
No sharp edge
-
Simple and fast operation

SafeSeal - High Containment Clip System up to OEB 4*
The SafeSeal closure is a new PA double crimp system with an axial closing mechanism and includes a pressing and cutting tool.
The SafeSeal closure is pulled manually over the bag and pressed together with special closing pliers. The crimp is then separated with a cutting tool. In addition, the crimp can be opened by cutting the outer closing mechanism with the cutting tool. That way, the foil can't be damaged.
-
Simple and safe operation
-
Closure system kit consisting of the SafeSeal closure, a pressing and a cutting tool
-
High level of containment (<1 µg/m3)
* Depending on powder characteristics and operational procedure

Liner Specifications
The liner can be supplied pre-folded in various sizes, produced in an ISO class environment and delivered in a PE bag. Fold height and length depend on the foil thickness.
CLS liner film qualities and design
Film type 1: LD-PE FDA with 1 % static inhibitors, migrating (non clean room)
Film type 2: LD-PE pharma (only clean room confection)
Film type 3: LD-PE pharma (clean room extrusion and confection); permanent antistatic
Films with customer-specific requirements can be procured and produced on request as well
Liner cartridge characteristics
-
LD- PE material
-
Foil width from 400 to 970 mm
-
Foil height 200 / 250 / 400 mm
-
Liner thickness from 50 - 150 microns
-
Dissipative
-
FDA approved
Options
-
γ-Sterilization after confection
-
Antistatic grid matrix; print 2 sides; color green
Further CLS system accessories include:
> Vent filter > Sampling > Safety cabinet > Welding machine > Bellows
Vent Filter / Inflate and Deflate Function
In order to prevent a pressure increase in the system when powder is charged into bags, the system must be able to breathe in order to evacuate the gas brought in.
Especially when precise filling is relevant, avoiding any pressure in the bag is very important as it could influence the scale.
When handling toxic, irritant or dust explosive powders, it is also imperative to avoid dust propagation into extraction lines which could lead to cleaning issues, operator exposure risks or even possible blockages due to powder accumulation in downstream equipment.
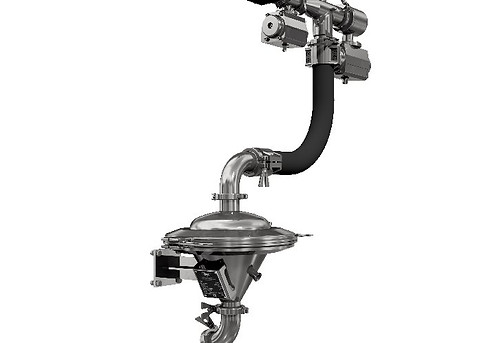
Dec's highly efficient, automated Vent Filter based on PTS filtration technology which can be connec...
Dec's highly efficient, automated Vent Filter based on PTS filtration technology which can be connected to the filling line.
It includes an automatic back-flushing system by compressed gas (air or nitrogen) and a connection to an extraction system. The system is 100% cleanable by back-flushing the membrane with a cleaning solution and through an integrated spray nozzle.
The inflate and deflate function inerts the bag and controls the pressure inside the system. A pressure sensor can be added in line for automated pressure control during the filling process.
The vent filter can be supplied in various sizes and materials to suit specific process requirements.
Sampling
It is often mandatory to take samples during the filling procedure at different intervals.
When considering a contained and GMP compliant filling system, it is not possible to reopen the packaging to take the samples manually afterwards.
Dec provides fully contained solutions to take samples either directly out of the filling system with MPTS or with a mechanical sampling device installed in the charging tube.
The sampling system is fully automated and synchronized with the filling operation able to draw samples at given intervals. The bottle is placed in a safety cabinet or a glove box for safe removal.

Safety Cabinet
For additional containment around the CLS for higher operator safety in case of liner failures, Dec can provide a safety cabinet around the filling station.
The cabinet includes an access door for the drum installation and removal and gloves to prepare the liner.
The system can be cleaned with a spray gun and comprises a drainage point.
For even higher containment, the cabinet can be equipped with a pass box on the side to enter and remove the drums.

Welding Maschine
Instead of a clips system, a welding machine can be used for the sealing of the bags.
The welding system can be integrated in the support frame.
This arrangement enables welding and cutting of the liners in a single operation.
-
Various length depending on liner size
-
ATEX zone 1 /21
-
OEB 4 containment

Bellows
Specific weight compensator to prevent any scale influence.
Triclamp connections are moulded to the bellows guaranteeing a tight connection and efficient cleaning.
-
Size DN 50, 100, 150, 200
-
Material : EPDM, Viton
-
Antistatic, FDA
